Von Richard Waldherr im Februar 2005
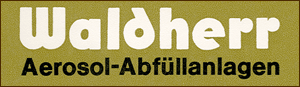
Johann Waldherr baute 1912 ein Wohnhaus mit einer Werkstatt über zwei Etagen im Hinterhof der Alphornstraße 46 in Mannheim und gründete die Johann Waldherr Kunstschmiede und Bauschlosserei.
J. W. war unter anderem 12 Jahre als Meister und Werkleiter bei der Kunstschmiede Joseph Neuser tätig und war entscheidend an der Fertigung der von Professor Götz, Karlsruhe, entworfenen Toranlage des Klinikums Mannheim beteiligt, welche 1900 auf der Weltausstellung in Paris mit einer Goldmedaille ausgezeichnet worden ist.
Weil nach dem ersten Weltkrieg, ausgelöst durch die Wirtschaftskrise, die Nachfrage an prunkvollen Toren und Gittern stagnierte und so den Kunstschmieden keine Existenz mehr bot, übernahmen Mitte der Zwanziger Jahre die Söhne Wilhelm und Richard, auch als Kunstschmiede ausgebildet und im Betrieb tätig, die Fertigung von Apparaten, wie Gaskessel, Wärmeschränke und Bauteile für Zentralheizungen, sowie Betten und Sitzmöbel aus Stahlrohr. Hinzu kamen Verpackungsbehälter aus Metall, sowie Kistenbeschläge, Griffe und Verschlüsse für die Holzindustrie.
Der Betrieb, der nun unter Johann Waldherr Apparatebau Metallwaren firmiert, expandiert, die Werkstätten sind zu klein. Deshalb werden 1934 Hallen des Mälzerei- Gebäudes und den anschließenden Nebengebäuden der ehemaligen Badischen Brauerei angemietet, die Platz für zehn Abteilungen boten.
Der Raum für die Zuschneiderei liegt im Erdgeschoss zwischen der Fa. Gerberich und dem Auslieferungslager der Erdal Wachs- und Schuhcreme Fabrik. Dort stehen die schweren Scheren mit welchen die Mäntel und Seitenteile für die Einsatzfertigung (für Munitionskästen aus Holz) geschnitten werden. Ein Lastenaufzug wird eingebaut um die Zuschnitte in die erste Etage zu befördern. In der Halle der ersten Etage über Gerberich befinden sich der Werkzeugbau und die Stanzerei. Dort stehen die Werkzeugmaschinen sowie 18 Werkbänke zur Herstellung der Stanz- und Presswerkzeuge, und schlussendlich 60 Exzenterpressen mit Presskräften von 40– 80 Tonnen. Die Dreherei mit den Dreh– und Fräsmaschinen ist im Turmbau platziert. Auf dem Vorplatz steht eine Walzmaschine zum Glätten der Bandeisenringe zum Verarbeiten in der Stanzerei. Über der Zuschneiderei befindet sich die Betriebs- und Vorrichtungsschlosserei. Hier arbeiten die Maschinenschlosser, Rohrschlosser, Spengler und Elektriker.
In der Behälterfertigung in der zweiten Etage über der Stanzerei werden die Einsätze auf speziellen Vorrichtungen geschweißt und mit Prüfeinrichtungen auf Dichtheit kontrolliert. Dort sind anfangs auch für die Verwaltung fünf Büroräume abgeteilt. Die Lackieranlage für die Einsätze befindet sich im Turmbau über der Dreherei und nebenan über der Schlosserei die Versandabteilung sowie das Schraubenlager. In der Halle der dritten Etage befindet sich die Montageabteilung. Die Einrichtungbesteht aus Bohr– Punktschweiß– Falz– Bördel– Niet– Gewindeschneidmaschinen und Montagepressen. Eine weitere Lackieranlage für Einbrennlacke ist im Turmbau. Nebenan über dem Versand stehen die Tauchlackieranlagen für die Beschläge, Griffe und Verschlüsse, sowie die Lack– Einbrenn- und Trockenöfen.
In der vierten Etage des Turmbaues befindet sich die Autogen– und Elektroschweißerei für die Verschlussösen. Auf dem Vorplatz stehen zwei Acetylengasbereiter mit je 4 Kubikmeter Volumen und eine Batterie von je 4 Sauerstoff- Flaschen, welche im Wechselbetrieb die Schweißbetriebe kontinuierlich über ein Rohrnetz mit Schweißgas versorgen. Ebenfalls angemietet sind die Hallen in der ersten und zweiten Etage des Gebäudes neben der Mälzerei. Hier befinden sich die Wasch- und Umkleideräume sowie die später eingerichtete Werkskantine, welche im Schichtbetrieb für die Belegschaft das Mittagessen bereitet. Auch die Gewölbekeller unter der Mälzerei werden benutzt. Hier steht eine Anlage mit je zwei Druckluftkompressoren und Druckkessel mit einem Volumen von 8 Kubikmeter. Sie versorgt die pneumatisch betriebenen- Kantmaschinen und Schweißvorrichtungen mit Druckluft. Eine Reibspindelpresse mit einer Presskraft von 120 Tonnen ist hier aus statischen Gründen aufgestellt (deren Fundamente sind heute noch vorhanden). Das Lager für die Stanz- und Presswerkzeuge, sowie die Kistenschreinerei haben hier ebenfalls Platz gefunden. Sonst werden hier die schweren Bandeisenringe für die Beschläge, Griffe und Verschlüsse gelagert. Zu deren Förderung von der Hofebene aus wird auf der Stirnseite des Mittelschiffes eine Materialrutsche eingebaut. Anfang des Krieges werden alle anderen Kellerhallen der Brauerei, ausgenommen der zwei Keller von Perl und Treiber, als Luftschutzräume genutzt. Gasschleusen und ein Sanitätsraum mit Liegeraum werden eingebaut.
Tonnenschweres Material werden auf Hubgestellen, teils mit Kisten versehen, auf hydraulisch betätigten Hubwagen über die Etagen bewegt. Auch die voluminösen Einsätze müssen abtransportiert werden. Der vorhandene Aufzug ist deshalb überlastet. Auf der nördlichen Stirnseite des Mälzereigebäudes wird über vier Etagen ein außenliegender Aufzug gebaut. Dieser ist so ausgelegt, dass auch die Hofebene und die verschiedenen Pritschenhöhen der Fahrzeuge angesteuert werden können. Weil die Fertigung der Einsätze wegen ihres Volumens in größeren Mengen nicht im Hause gelagert werden können, werden diese vom Pferdefuhrwerkbetrieb Hamel laufend an die Bahnhöfe Neckarstadt und Käfertal transportiert und in Eisenbahnwaggons verladen.
J.W. übergibt 1936 seinen Söhnen den Betrieb
Das Unternehmen beschäftigt in den besten Zeiten bis zu 800 Leute, vorwiegend Frauen. 12 Meister stehen den Abteilungen vor. Es wird in Schichten gearbeitet. Ab 1940 werden von der Behörde 25 französische Kriegsgefangene zugeteilt, welche sich ohne Bewachung frei im Areal bewegen. Sie wohnen in einer Baracke die auf dem Betriebssportplatz Ecke Röntgen– Cheliusstraße errichtet wird. (Heute steht dort ein Haus für Krankenschwestern des Klinikums)
Gefertigt werden luftdichte Einsätze verschiedener Größen für Pulver- und Munitionskisten aus Holz, sowie die hierfür benötigten Beschläge, Schalengriffe und Verschlüsse. Diese Produkte werden an die Holz- und Möbelfabriken im ganzen Reich geliefert.
Tragbüchsen für Gasmasken, Geschosskörbe aus Holz und Metall, Geschossbehälter für die 2,7 cm Panzerabwehrkanone, Behälter für das Geschoss der 8,8 cm Fliegerabwehrkanone, sowie luftdichte Blechkoffer für die Truppe in Afrika, werden an die Wehrmacht geliefert.
Ein Großhandel wird angeschlossen. Verkauft werden die zur Befestigung der Kistenbeschläge, Griffe und Verschlüsse benötigten Holzschrauben, sowie andere Befestigungselemente. Waldherr ist der größte Abnehmer des Deutschen Holzschraubenverbandes.
Die laufende Fertigung, sowie die Endprodukte für die Wehrmacht, wird von Feuerwerkern der Heeresabnahmestelle kontrolliert. Diese ist ebenfalls in einem Gebäude der Brauerei stationiert, von Waldherr unterhalten und ist darüber hinaus für andere Betriebe im Mannheimer Bezirk und der Umgebung zuständig.
Bombenabwurf in der Nacht vom 5./ 6. September 1943: die größte Katastrophe, die die Stadt erlebt. Auch die Brauerei ist schwerst betroffen. Eine Vielzahl Stabbrandbomben entfacht über die ganze Mälzerei und den anliegenden Gebäuden ein verheerendes Feuer. Die vielköpfige Brandwache konnte das Feuer leider nicht aufhalten. Die dritten und vierten Etagen mit den Holzböden und den Dächern sind abgebrannt. Deren Schutt und Asche, sowie die ausgebrannten Maschinen, Vorrichtungen, Mobiliar und Teile der Fertigung bedecken die Maschinen der Stanzerei, Werkzeugbau und Schlosserei. Die Betondecken der ersten Etage halten dem Feuer und der Belastung stand. Die Werkskantine, die Wasch- und Umkleideräume, sowie der Außenaufzug sind aus- und abgebrannt. Lediglich das Turmgebäude mit den Maschinen, Einrichtungen und Anlagen sowie der Innenaufzug sind nahezu unversehrt. Glücklicherweise sind die drei Sprengbomben außerhalb der Gebäude eingeschlagen und haben die Fassade nur leicht beschädigt.
Das scheint zunächst das Ende der Firma Waldherr und dem größten Teil der Brauerei zu sein. Die Geschäftsleitung beschließt jedoch sofort den Wiederaufbau und erklärt in wenigen Wochen die Fertigung wieder aufnehmen zu können. In der ausgebrannten Halle von Erdal wird ein Notbüro eingerichtet. Ein Architekt wird hinzugezogen. Die Statik der Fassaden, der Säulen und Träger der Etagen ist noch intakt. Die Behörde genehmigt die Dächer über der ersten Etage. Man plant jedoch diese eine Etage höher zu setzen, um dann später die Decken der zweiten Etage einzubauen. Spontan sind befreundete Holzfirmen bei der Beschaffung der benötigten Balken und Bretter behilflich. Während der Dacharbeiten werden die Hallen vom Schutt befreit, und durch die Fensteröffnungen auf die Röntgenstraße geschaufelt. Dort liegt er noch weit über ein Jahr nach Kriegsende. Auch die Betonfertigdecken für die zweite Etage werden schon geplant. Die Fenster neu verglast, soweit defekt, durch Neue ersetzt. Die Aufbauarbeiten werden weitestgehend vom eigenen Personal getätigt. Die Maschinen der Stanzerei, des Werkzeugbaus und der Schlosserei, welche vom Schutt bedeckt waren, haben den Brand relativ gut überstanden, werden nun gereinigt und soweit nötig instandgesetzt. Für die ausgebrannten Maschinen wird Ersatz bestellt. In Tag und Nachtarbeit werden Vorrichtungen zur Fertigung der Einsätze neu konstruiert und hergestellt. Der Werkzeugbau als Schlüsselabteilung, sowie wichtige Maschinen der Stanzerei, der Montage und die Kantmaschinen für die Einsätze werden in zwei von drei Schiffen des Kellers verlegt. Die Werkskantine wird wieder aufgebaut. Für die ausgebrannten Büros, welche sich in der zweiten Etage des Mälzereigebäudes befanden, werden in einer Halle der an der Mälzerei anliegenden Gebäude 8 Räume abgeteilt.
Das fast Unmögliche ist geschafft. Die Fertigung läuft wieder auf Hochtouren, nur unterbrochen durch die immer öfter gegebenen Fliegeralarme, wobei jedes mal die nun mobilen Schweißvorrichtungen, die unersetzlichen Büromaschinen und wichtige Akten in den Keller befördert werden. Man befürchtet, dass die Decken der Schutzräume, welche sich zum großen Teil unter der Hoffläche befinden, den Sprengbomben nicht standhalten würden und suchte nun Schutz in den Kellerräumen unter der Mälzerei. Bei weiteren Luftangriffen auf Mannheim bleibt die Brauerei verschont.
Das baldige Kriegsende ist vorauszusehen, der Betrieb wird eingestellt. Man widersetzt sich dem am 19. März von Hitler angeordneten Nerobefehl, wonach alle Fabrikanlagen zerstört werden müssen. An jeder Maschine wird ein spezifisches Teil für deren Betrieb entfernt und mauert diese in einer Nische im Keller ein.
Der Krieg ist zu Ende. Die Maschinen werden wieder aufgerüstet. Wegen der Parteimitgliedschaft der Gesellschafter steht der Betrieb unter Treuhandschaft, so ist deren Tätigkeit weitestgehend beschränkt. Der Betriebsrat ist kommunistisch beeinflusst und wenig behilflich bei der Umstellung auf ein neues Programm. Auf legale Weise ist kaum Material für eine Fertigung zu beschaffen. Lockenwickler, Haarklammern, Maschinchen zum Selbstdrehen von Zigaretten, Deckel für Konservendosen, Bett und Fensterbeschläge und anderes Zeug wird gefertigt.
30. Juni 1948
Mit dem Tag der Währungsreform erlischt die Treuhandschaft. Nun kommt das Finanzamt und aktiviert nach einem Kontrollratgesetz die Verluste wegen des Brandschadens und Forderungen an das Reich und erzwingt eine Nachzahlung über 100.000 DM, wofür ein Bankkredit aufgenommen werden muss.
Das Unternehmen steht fast vor dem aus. Das Personal wird reduziert, teils an befreundete Firmen ausgeliehen oder entlassen. Die Werksküche, der Speisesaal und die darunter liegenden Büros werden aufgegeben. Die Kleiderfabrik Lissner und Rösner übernimmt die Räume. Niderehe baut nun für Waldherr drei Büroräume in der zweiten Etage über der Schlosserei.(deshalb befinden sich dort die drei großen Fenster in der Frontfassade).
Glücklicherweise steht der gut gerüstete Werkzeugbau mit einigen hoch qualifizierten Werkzeugmachern zur Verfügung und ist die Vorrausetzung für den Neuanfang.
Auch die Söhne von Wilhelm Waldherr, Richard und Norbert, als Werkzeugmacher ausgebildet, sind nun in der Firma tätig.
Gefertigt werden nun Kernbleche für Kleintransformatoren verschiedener Typen und Größen mit Befestigungswinkeln, Blechgehäusen, Lötleisten- und Platten, für die Elektroindustrie. Chassis und Skalenelemente für die Radiogeräte- Firmen. Geliefert wird in das ganze Bundesgebiet. Für Siemens in Speyer werden umfangreiche, präzise Stanz- und Pressarbeiten für Fernmelde- Relais und Verteilerplatten ausgeführt.
1951
Über eine Ausschreibung der US Army von 50.000 Sperrholzkoffer mit Einsätzen erhält Waldherr, für einen Metallbetrieb ungewöhnlich, einen Auftrag über 10.000 Einheiten. Sofort werden die Werkzeuge für die Beschläge und Verschlüsse gefertigt. Für die hierfür benötigten Befestigungsnieten und Zylindervorhängeschlösser lässt sich Waldherr bei den Vorlieferanten 50.000 Garnituren reservieren. So müssen die Mitlieferanten außer den Beschlägen und Verschlüssen auch das Befestigungsmaterial und die Schlösser bei Waldherr kaufen.
Die große Halle in der zweiten Etage wird für die Fertigung vorbereitet. Die Vorrichtungen zum Schweißen der Einsätze werden aus dem Keller geholt, für das Zusammennageln und Nieten der Holzkoffer umgebaut. Eine Lackieranlage mit Hängebahn zum Trocknen der Koffer nimmt 1/3 der Hallenfläche ein. Eine Zuschnittsäge wird gekauft. Ein Schuppen hierfür und zur Lagerung der angelieferten Sperrholzplatten auf der gegenüberliegenden Hofseite gebaut. Wiedereinmal wird bei Tag und Nacht und an Sonn- und Feiertagen gearbeitet.
Am Vorabend des angesetzten Liefertermins wird die Nullserie mit den Werkzeugmachern und Schlossern zusammengenagelt und genietet. Am nächsten Morgen übernehmen 40 über das Arbeitsamt eingestellte Schreiner die Arbeitsplätze an zwei Fertigungsstraßen und abends hängt die geplante Tagesfertigung von 200 Koffer lackiert und versandbereit an den Haken der Trockenbahn. Die Lieferungen, auch an die Mitlieferanten, werden nun anstandslos, fristgerecht und höchst profitabel abgewickelt. Was Viele nicht für möglich hielten. Von da an ging es bergauf.
1954
Für die Schmalbach- Blechwarenwerke, Zweigwerk Karlsruhe, wird ein Spannringverschluß für mehrfach verwendbare Konservendosen entwickelt, patentiert und gefertigt. Der Artikel kommt bei dem Verbraucher gut an. Über zweihunderttausend Ringe werden jährlich geliefert. Das Verschlusssystem wird für Chemikalien- Lack- und Farbeimer übernommen. Eine Fertigung von Ringen bis zu 300 mm Durchmesser wird aufgezogen zur Lieferung an weitere namhafte Blechwarenwerke im Bundesgebiet (Marktanteil 75%). Auch in die Schweiz und nach Frankreich wird geliefert.
In der Halle im Erdgeschoss (vorher von Gerberich genutzt), lagern Tonnen von Weiß- und verzinkten Blechen welche mit schweren Scheren und Rollenscheren zu Streifen für die Ringfertigung geschnitten werden. An der Decke befinden sich Kranbahnen um das Material zu bewegen. Die Verschlussteile werden in der Stanzerei mit automatischen Pressen gefertigt. Aus Kostengründen werden die Verschlüsse in der Behinderten Werkstatt Neckarau, sowie in den Justizvollzuganstalten Mannheim und Frankenthal, mit von Waldherr beigestellten Vorrichtungen, zusammengenietet. In der großen Halle der zweiten Etage werden auf umgebauten Bördelmaschinen die Blechstreifen profiliert, zu Ringen gerollt und mit den Punktschweißmaschinen die Verschlüsse befestigt. Über 20 Punktscheißmaschinen werden betrieben. An einem Karusselltisch montieren 20 Frauen die Konservendosenspannringe, welche anschließend in Schutzlack ge-taucht und im Brennofen getrocknet werden. Die Spannringe sind nun wesentlicher Umsatzträger. Die wenig ertragreiche Fertigung der Kernbleche mit Zubehör wird aufgegeben.
1956
In Pionierarbeit wird für europäische Verhältnisse geeignetes Verfahren zur Dosierung von Flüssiggas im geschlossenem System entwickelt, Vorraussetzung zum Bau von Füll- und Verschließmaschinen für Sprühdosen. Prototypen werden gebaut und bei den Siegelwerken in Köln zur Füllung der Flit- Insektensprühdosen mit Erfolg getestet. Nun wird die erste automatische
Sprühdosenabfüllmaschine Europas gebaut, auf der internationalen Verpackungsmesse in Düsseldorf ausgestellt und findet unter den Experten großes Interesse. Schwarzkopf übernimmt die Maschine und füllt im Werk Wassertrüdingen Taft-Haarsprühdosen. Weitere namhafte Kunden konnten gewonnen werden. Waldherr ist nun im Geschäft.
Ein Büro für die Konstrukteure wird angebaut. Mehrere Unterlieferanten fertigen die benötigten Drehteile, Maschinenelemente und Gestelle. In der ehemaligen Zuschneiderei werden die Maschinen, teils bis zu 5 Meter lang und bis zu 3000 kg schwer, montiert. Geliefert werden die Maschinen an kosmetische- und chemische Werke erster Adressen im Bundesgebiet und Ausland.
Firmiert wird nun unter Johann Waldherr Stanz und Presswerk Maschinen und Apparatebau.
Das Flüssiggastreibmittel für Sprühdosen dient auch als Kältemittel für Kühlschränke. Von der Industrie aufgefordert entwickelt Waldherr eine Abfüllanlage für Kühlaggregate und liefert diese an Kühlschrankfabriken in Deutschland, nach Frankreich, England, Dänemark und Schweden.
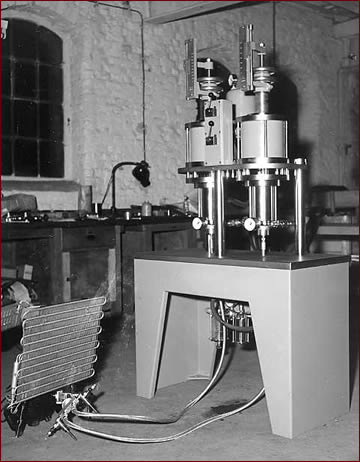
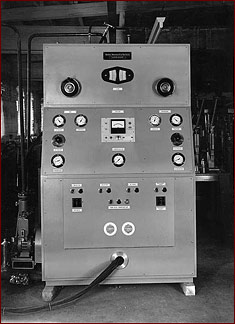
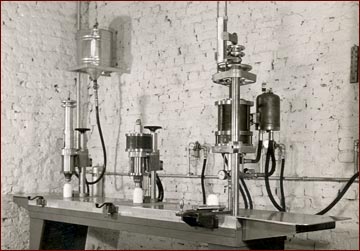
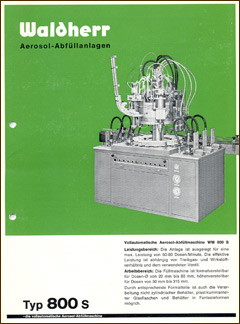
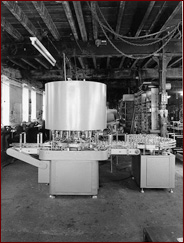
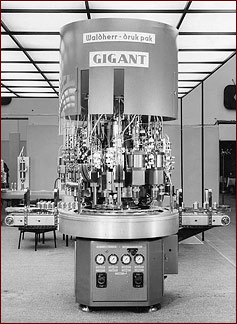
Sprühdosenabfüllmaschine für Doppelschritt-Rundtakt
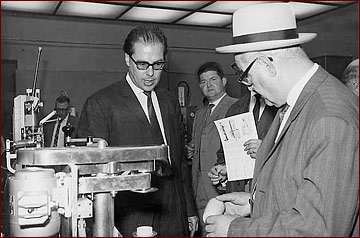
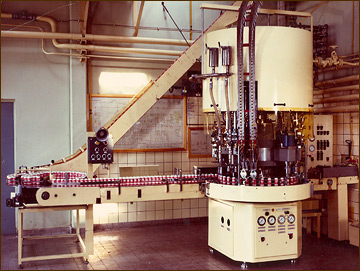
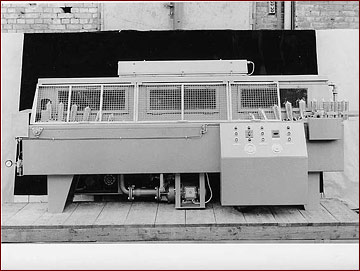
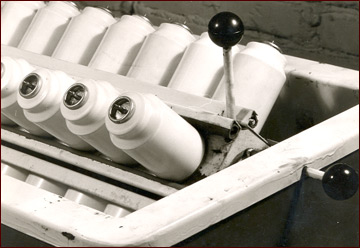
Auch ein Spezial-Schraubverschluss für Kunststofftuben wird entwickelt und patentiert. Zur Fertigung wird die Lizenz an ein Kunststoffwerk vergeben und die hierfür benötigten Abfüllmaschinen gefertigt.
Durch erhebliche Umsatzrückgänge in der Sparte Spannringverschlüsse – 1973 durch die Ölkrise ausgelöst – Probleme wegen der Vorfinanzierung einer kompletten Füllanlage an die DDR (Auftragswert ca. 1 Million DM), welche als Generalunternehmen, gefertigt, termingerecht geliefert und mit Erfolg ohne Abstriche in Betrieb genommen werden konnte, geriet die Firma in finanzielle Engpässe. Diese Anlage galt als Pilot Projekt für den Osten. In Folge konnte ein Auftrag über 10 Anlagen dieser Dimension mit der UDSSR abgeschlossen werden. Die Badische Bank war unter den gegebenen Umständen nicht bereit dieses Objekt zu finanzieren. Im Gegenteil sie kündigte umgehend die bestehenden Kreditlinien.
Das bedeutete 1974 das Aus für die Johann Waldherr O.H.G.